Film Oil
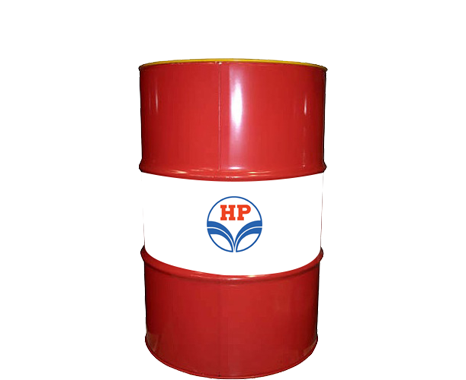
HP STEEL EP 100
BEARING OILS FOR STEEL PLANTS
Meets specifications:
It meets the specifications of MORGAN CONSTRUCTION CO., USA. the worldwide manufacturer of No–Twist Rod Mills
Application areas:
This oil has very good and demulsibility characteristics and hence it is recommended for use in all Morgoil bearings in no-twist rod mills in Steel Plants. It is also recommended in applications where severe load conditions are encountered.
Performance benefits:
- Excellent extreme pressure characteristics
- Very good oxidation and chemical stability
- High FZG rating
- Excellent demulsibility
- Good resistance to foaming
- Full protection against rusting
Special Features
HP STEEL EP 100 is a specially formulated premium bearing and hydraulic oil to meet the specific requirements in steel plants. It meets extreme pressure and good demulsibility requirements in bearing lubrication.
It is blended from premium quality base stock and selected grades of anti-oxidants, anti-rust, demulsifier, defoamant, anti-rust and mild anti-wear additives. This oil is suitable for use in conditions where very good load bearing ability along with excellent demulsibility characteristics are critical requirements. This product has good wettability and high film strength providing extra rust protection and eliminating scuffing and scoring of the bearing. It has a good water separating ability which is retained at a high level during extended use in water quenching conditions.
Physico-chemical properties
Characteristics | Typical value | Test Method |
---|---|---|
VISCOSITY GRADE | ISO VG 100 | ISO 3448 |
API GRAVITY | 28 | ASTM D 287 |
SPECIFIC GRAVITY @ 60/60° F | 0.896 | ASTM D 1298 |
POUR POINT, ºC | -15 | ASTM D 97 |
FLASH POINT, COC, ºC | 228 | ASTM D 92 |
VISCOSITY @ 40°C, CST | 93.2 | ASTM D 445 |
VISCOSITY @ 100°C, CST | 10.7 | ASTM D 445 |
VISCOSITY INDEX | 98 | ASTM D 2270 |
COLOUR | 1.5 | ASTM D 1500 |
RUST TEST | Pass | ASTM D 665 |
BATTERY JAR RUST TEST | pass | MOBIL |
DEMULSIBILITY | 40-37-3(10 MINUTES) | ASTM D 1401 |
DEMULSIBILITY | ASTM D 2711 | |
TOTAL FREE WATER, ML | 38 | |
DYNAMIC DEMULSIBILITY ENDURANCE | RUN AT CLARK LAB | |
MAX. % WATER IN OIL | ||
AFTER CENTRIFUGING | 10% | |
MAX. % OIL IN WATER | ||
AFTER CENTRIFUGING | 1 | |
COPPER STRIP, CORROSION, AT 1000C FOR 3 HOURS | 1A | ASTM D 130 |
Characteristics | Typical value | Test Method |
---|---|---|
4 BALL EP TEST, WELD LOAD, KG, | >160 | ASTM D 2783 |
4 BALL WEAR, 54°C, 1800 RPM, 20 KGS,1 HR, WSD, MM MAX | 0.25 | ASTM D 2266 |
RPVOT, MINIMUM MINUTES TO FAIL | 290 | ASTM D 2272 |
FZG EP TEST, PLS | 12 | DIN 51534 |
AIR RELEASE VALUE @ 50 ºC | 7.5 | ASTM D 3427 |
AIR RELEASE VALUE @ 75 ºC | 4 | ASTM D 3427 |
FOAM STABILITY, ML, AFTER 10 MIN SETTLING TIME | ASTM D 892 | |
SEQUENCE I | 0 | |
SEQUENCE II | 0 | |
SEQUENCE III | 0 |
PERFORMANCE BENEFITS
- Excellent extreme pressure characteristics
- Very good oxidation and chemical stability
- High FZG rating
- Excellent demulsibility
- Good resistance to foaming
- Full protection against rusting